轻量化是行业大势所趋
相关报道显示,我国石油对外依存度已经突破60%,成为世界第一大石油进口国。作为国民经济的支柱产业之一,我国工程机械行业的发展正面临着能源环保问题的巨大压力,“节能环保”的诉求日益成为全社会关注的焦点,如何用更小的能耗制造更多的效益,成为行业共同关心的话题。在这一大背景下,工程机械轻量化技术的发展开始受到行业各方的重视,切实提高工程机械轻量化技术水平,成为行业技术重要发展方向之一。
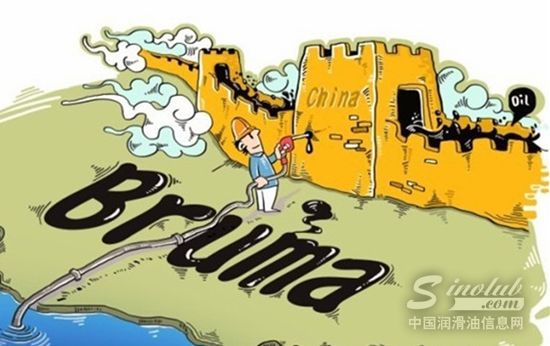
作为融入汽车和机械基因的润滑油第一门户,行业分析师指出,工程机械的轻量化,对于减少钢材消耗以及相应生产、运输等环节的能源消耗,降低作业过程中的能耗与废气排放、降低噪声等都具有直接影响,节能减耗的潜力巨大。此外,轻量化的意义不仅仅在于节能减排。机械重量变轻,对于整体的操纵性、稳定性、碰撞安全性等都大有裨益,具有输出功率高、噪声小、振动低、操控可靠等诸多优点。
轻量化技术实力 国内外差距明显
在应对轻量化的时代要求上,我国工程机械行业和国外先进水平相比存在着明显的差距。具体而言,欧美国家工程机械在轻量化技术应用与研究上起步较早,发展相对成熟。在轻量化材料使用和制造方法方面,国外普遍做法是借鉴材料科学与材料加工科学的研究成果,将高强钢等新型材料应用于零部件设计与制造中,在保障强度的基础上,有效减轻零部件自身载荷,达到轻量化的目的。不仅如此,一些企业还把“轻量化”的概念运用于产品模型检验中,拓宽了轻量化的运用领域。以卡特彼勒为例,这家行业巨头运用3D打印技术生产轻量化履带式推土机连接组件,使员工无需等待沉重的锻造零件就可以执行相关检验程序。这项看似不起眼的轻量化调整,每年为卡特彼勒节省16万美金。
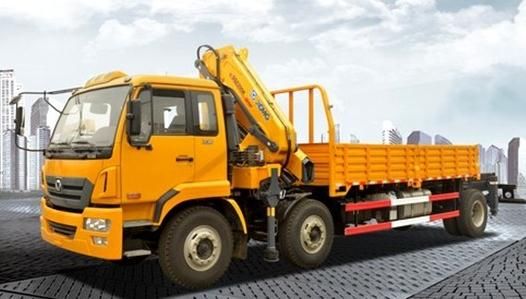
至于我国,工程机械行业在钢结构设计上沿袭前苏联经验,设计理念十分保守,具体表现为过度重视安全因素,致使机器结构笨重,性能较差。此外,我国工程机械企业自主创新能力薄弱,设计周期长,可选方案少,在涉及产品细节结构的智能技术上更是缺乏应有的深度,这一切都导致我国轻量化技术水平落后于世界先进水平,不免令整个行业扼腕叹息。
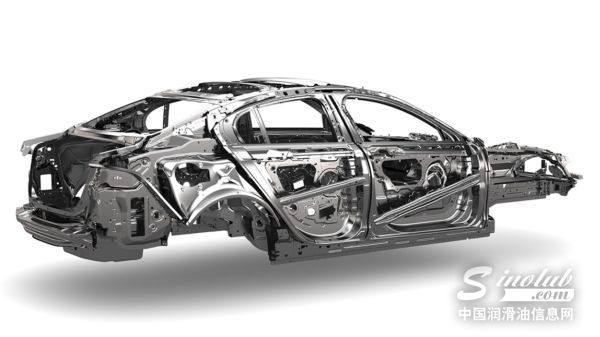
相较于工程机械行业的迟缓,民族汽车工业在轻量化技术方面已经先行一步。国内开发的高强度钢设计制造技术,其零件强度可达800MPa以上,减重潜力超过30%。此外,铝合金、镁合金、高强度纤维材料等材料也被运用于民族汽车工业,发达国家新兴的工程塑料材料,其应用前景也被国内汽车业界人士一致看好。可以说,汽车轻量化技术的进步为工程机械行业的轻量化提供了有益的参考和借鉴,但相关材料还需要针对工程机械自身特点进行研究,尤其是针对不同工况的要求具体分析。
实践效果明显 轻量化前景可期
在实践中,一些民族品牌厂商开始采用轻量材料代替传统钢材,为行业做了有益的探索和尝试。如中联重科开发的80m碳纤维臂架混凝土泵车,采用了碳纤维复合材料、优化结构,同时采用小一级底盘(即60m钢臂架混凝土泵车底盘)等工程机械轻量化技术。在保持原有结构性能情况下适当使用玻璃纤维增强塑料(玻璃钢)做成车身骨架,比原有传统钢质车身减重20%~30%。
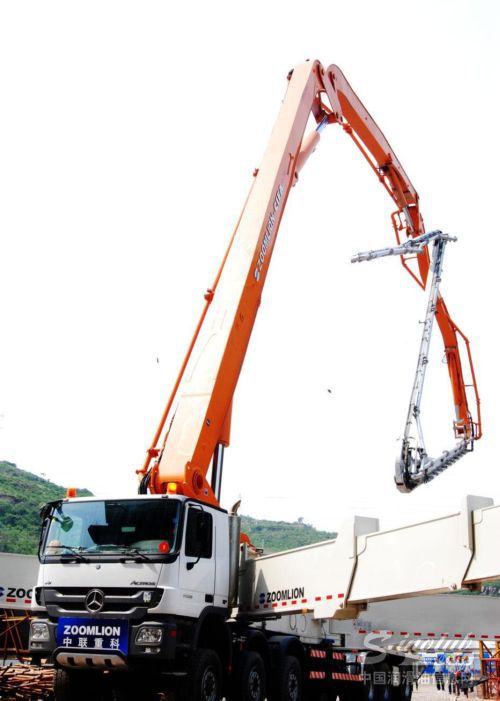
除了新材料的应用,另一些民族企业选择另辟蹊径,通过结构设计的优化调整实现轻量化的目标。如采用单发动机系统,整车共用一台发动机,为此还带动了新型变速箱、传动器开发和发动机能量管理等一系列技术的革新。与传统双发动机起重机液压系统传输动力不同,单发动机系统通过机械系统传导动力,重量更轻,效率更高。这辆应用了轻量化技术的起重机,和传统的徐工QAY500相比,整车总质量降低了约800kg,性能却提高了5%到10%。
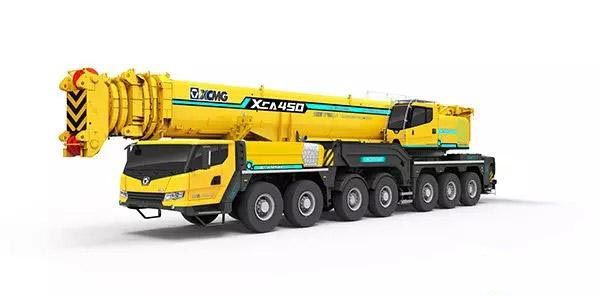
无论是新材料的运用还是结构的优化调整,自主品牌正在以扎实的步伐推进产品轻量化的应用。应当看到,轻量化已成为当前工程机械行业的一种发展趋势,通过轻量化技术开发节能环保的绿色产品已成为诸多工程机械制造商的发展战略之一。展望未来,随着行业逐渐突破轻量化的技术难题,工程机械轻量化将愈发成为业界的主流趋势,而自主主流工程机械制造商也已经完成了由中低端产品向中高端产品的过渡,拥有较齐全的中高端产品线,这也为轻量化产品的生产奠定了重要基础。
综上所述,工程机械轻量化对产品节油、减排、提高性能、乃至全行业的健康发展都具有重要的意义,也是现代工程机械行业技术的重要发展趋势之一。轻量化设计通过对工程机械结构和形状的设计优化,应用先进的加工技术和轻量化材料来实现整体机械的降重,还要综合考虑高动力输出、低噪声、低振动、良好操控性和高可靠性。令人欣喜的是,轻量化技术在实际发展中并不孤单,随着工程机械多功能化、智能化等技术的兴起,工程机械产品正朝着微型化、大型化、系列化的方向发展。工程机械轻量化技术的发展并不孤立,它与上述技术的发展紧密项链,共同服务于行业市场。